Weser Kurier
27.12.2016, von Carolin HenkenberensAus der Serie: „Von der Forschung zum Produkt (1)“
Bremer Wissenschaftler, Designer und Ingenieure haben einen Bollerwagen aus Hightech-Material entwickelt. Es ist ein Beispiel, wie Austausch zwischen Forschung und Wirtschaft funktioniert.
Organoblech ist ein Werkstoff der Zukunft. Einer, der normalerweise in der Luft- und Raumfahrt, in Flugzeugträgern, Schutzhelmen oder Fußballschuhen verbaut ist. Das Material ist leicht und zugleich stabil. Was aus dem Hightech-Material noch werden kann, zeigt eine Kooperation zwischen Wissenschaft und Wirtschaft aus Bremen: ein Bollerwagen.
Auf kleiner Ebene ausprobieren, was auf großer Ebene mal möglich sein soll: Das war die Idee, als sich im Winter vor vier Jahren eine Arbeitsgruppe um Daimler in Bremen traf. Denn auch die Automobilindustrie erforscht, inwiefern Organoblech Bauteile aus Stahl oder Aluminium ersetzen könnte. Autos wären damit um einiges leichter und könnten umweltfreundlicher fahren.
Als es losging, konnte sich noch niemand der Beteiligten vorstellen, was dabei herauskommen wird, erzählen die Beteiligten. Das sind neben Ingenieuren von Mercedes-Benz Forscher vom Faserinstitut, Studierende der Hochschule für Künste und Mitarbeiter des Martinshofs.
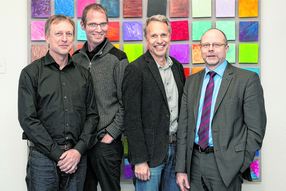
Kompetenzteam in Sachen Bollerwagen (vli.): Christoph Hoffmeister (Faserinstitut), Christian Hessling (Daimler), Prof. Andreas Kramer (HfK), Ahlrich Weiberg (Geschäftsführer Martinshof) (Christina Kuhaupt)
„Für soziale Zwecke wollten wir ein Produkt aus dem innovativen Material Organoblech entwickeln“, erklärt Christian Hessling die Idee. Hessling arbeitet als Prozessingenieur im Bereich Leichtbau bei Mercedes. Das Unternehmen lud die Studierenden zu einem Workshop ein. Es sollte etwas erfunden werden, das von Menschen mit Behinderung beim Martinshof montiert und vertrieben werden kann.
Da beim Martinshof bereits Möbel für Kitas hergestellt werden, sei die Wahl schnell auf ein Produkt für Kinder gefallen, sagt Hessling. „Am Anfang dachten wir an einen Stuhl“, sagt Andreas Kramer von der Hochschule für Künste. Er leitet den Masterstudiengang Material und Technologie, aus dem die Teilnehmer stammten. Kramers Studentengruppen arbeiten oft mit Unternehmen zusammen, um praktische Erfahrung im Produktdesign zu sammeln. Aus allen Entwürfen sei letztlich der Handziehwagen ausgewählt worden. Der Projektname sollte „Smarty“ sein – angelehnt an das englische Wort für „clever“.
„Wie groß sind Kinder in dem Alter eigentlich?“
Denn der Bollerwagen ist kein gewöhnlicher. „Durch den neuen Werkstoff Organoblech grenzt sich unser Wagen extrem von üblichen Bollerwagen ab“, sagt Christoph Hoffmeister, Vorstand des Faserinstituts. Das private Forschungsinstitut ist an die Universität sowie die Baumwollbörse angedockt und beschäftigt sich neben der Erforschung von chemischen und natürlichen Fasern auch mit Faserverbund-Technologien wie Organoblech. Organoblech ist Kunststoff, der mit einer Glasfaserstruktur verstärkt ist.
Der Bollerwagen sollte für acht Kinder im Alter zwischen einem und drei Jahren sein. Andreas Kramer berichtet von den praktischen Fragen, die sich den Studenten bei der Planung stellten: „Wie groß sind denn Kinder in diesem Alter eigentlich? Und wie schwer?“ Im Gespräch mit Erziehern und Pädagogen brachten diese ihre Ideen ein. Deshalb bekam der Wagen einen Verbandskasten.
Wagen wiegt gut 40 Kilogramm
Als die Entwürfe standen, hat die Arbeit für das Team bei Mercedes begonnen. „Wir haben das Fahrwerk mit dem Vierradkonzept entwickelt“, sagt Hessling. Auf das Fahrwerk ist ein Patent angemeldet worden. „Das Besondere an dem Fahrwerk ist der kleine Wendekreis. Man kann den Bollerwagen sogar problemlos in der Straßenbahn drehen.“ Die Abteilung Werkzeugbau bei Daimler hat zudem das Werkzeug zur Herstellung der Organoblech-Teile angefertigt. Die Sitze werden aus dem Organoblech umgeformt, wie Hoffmeister erklärt. Das bedeutet: Das Material wird erwärmt und anschließend in die passende Form gepresst. Diese Arbeit hat die Bremer Firma Trecolan übernommen.
Der fertig montierte Wagen wiegt gerade einmal gut 40 Kilogramm und kann etwa 120 Kilogramm tragen. „Aber wir wollen das Gewicht noch weiter reduzieren“, sagt Hoffmeister. Der Produktionstechnik-Student Patrick Nowakowski erforscht für seine Masterarbeit am Faserinstitut, wie die Radaufhängung des Wagens optimiert werden kann. Bislang besteht die noch aus Metall, aber sie soll durch ein leichteres Material ersetzt werden. „Für uns ist das Projekt keine Spielerei“, sagt Hoffmeister. „In dem Bollerwagen steckt viel Know-how.“
Drei Prototypen des Wagens sind mittlerweile fertig. In den Betriebskitas von Daimler in Bremen und Sindelfingen sowie der Kita von Airbus in Bremen werden sie im Langzeittest ausprobiert. „Die Reaktion der Erzieher und Kinder war super. Die Kindergärten fragen schon, ob sie einen weiteren bekommen können“, sagt Hessling. „Es gibt kein vergleichbares Produkt, in dem so viel Hightech steckt“, sagt Kramer.
„Es ist das Produkt des Martinshofes“, sagt Hessling. „Die Mitarbeiter des Martinshofs montieren und vertreiben den Wagen.“ Der Geschäftsführer des Martinshofes, Ahlrich Weiberg, sagt: „Der Wagen könnte weitere Beschäftigung für unsere Fahrradwerkstatt bringen in den Zeiten, in denen die Auslastung dort nicht so hoch ist.“
Neue Kooperationen sind entstanden
Als nächstes steht die Abnahme durch den Tüv bevor. Weiberg hofft, dass der Bollerwagen im Spätherbst des kommenden Jahres in die serielle Produktion gehen kann. Wie viele Wagen der Martinshof gedenkt, verkaufen zu können, darüber möchte Weiberg lieber nicht spekulieren. Den voraussichtlichen Preis des Wagens will er ebenfalls noch nicht nennen. Nur so viel: „Es wird sich im Rahmen der üblichen Marktpreise bewegen.“ Denn eine Anforderung an den Wagen sei auch gewesen, dass er nicht teuer wird, sagt Hoffmeister.
Und welches Resümee ziehen die Beteiligten aus der Kooperation? Mercedes-Benz habe viele Vorteile aus dem Kooperationsprojekt ziehen können, sagt Hessling. „Zum Beispiel sammeln wir Erfahrung in einer speziellen Anwendung des Leichtbaus.“ Im Nachgang ist eine weitere Kooperation zwischen Mercedes und dem Faserinstitut entstanden. „Wir erforschen, wie Kunststoffe und Metalle miteinander verbunden werden können“, sagt Hoffmeister. Auch das Faserinstitut und die Kunsthochschule haben ein neues Projekt angeschoben.
Die Zusammenarbeit hat nicht nur wirtschaftlich gesehen funktioniert. „Wir wurden inspiriert, anders zu denken“, sagt Hoffmeister. „Und zwar, dass Technik und Design kein Widerspruch sind.“ Kramer fügt hinzu, dass der Wagen wunderbar zeige, dass die Mitarbeiter des Martinshofs die Kompetenz haben, auch hochinnovative Hightech-Produkte zu bauen.
Link zum Artikel: http://www.weser-kurier.de/startseite_artikel,-Leichtbau-fuer-die-Luetten-_arid,1520841.html